Key Takeaways
- Circular Economy Starts from the Ground Up HHI’s deep understanding of the value chain—from household collection to industrial transformation—has enabled the company to build an ecosystem grounded in local realities, yet globally competitive.
- Integration is the Key to Recycling 2.0 HHI developed its own internal standards—cutting labour costs by 40% and logistics costs by 60%, while improving output quality.
- A Vision for Recycling 3.0 HHI is pushing toward a Recycling 3.0 paradigm—a smarter production and consumption system based on a “7+1 cycle.” This allows plastics to be infinitely valorised instead of polluting the environment.
- Profitability and Sustainability Can Coexist One of HHI’s most powerful assertions is that recycled plastics, when processed correctly, can be more valuable than virgin plastics.
- Real-World Learning Must Bridge Industry and Academia Effective learning isn’t just technical—it’s experiential, systemic, and outcome-driven.
Few dare to innovate and even fewer survive in industrial recycling.
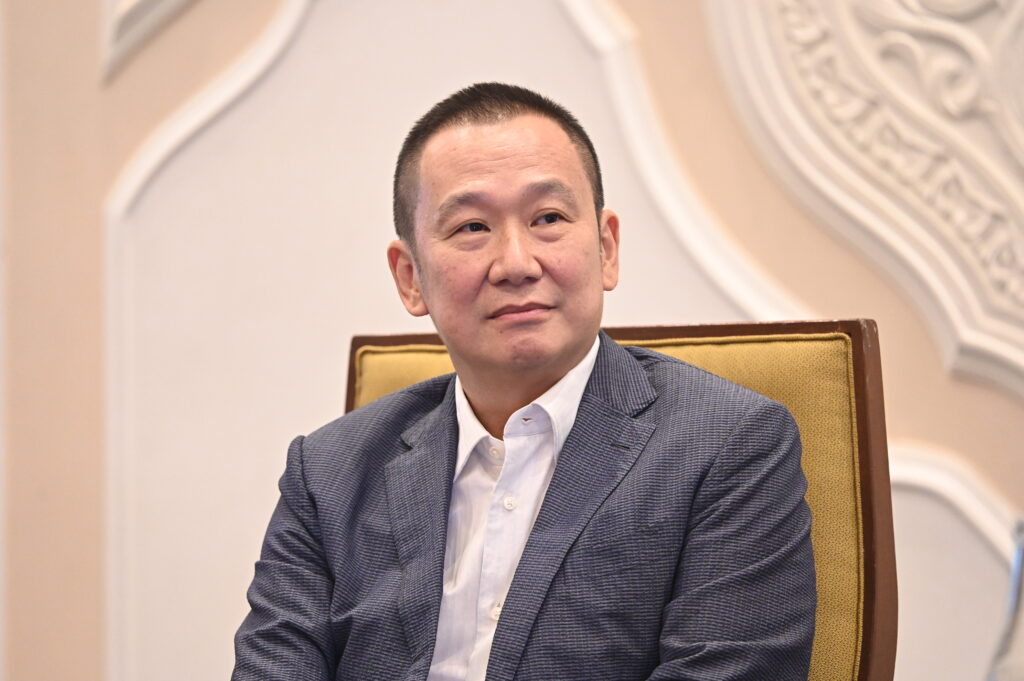
Yet, Seah Kian Hoe (“Kian”) has done both. As the Founder and CEO of Heng Hiap Industries Sdn Bhd (HHI), Kian has spent over two decades turning what society discards into value, transforming Malaysia’s plastic waste problem into an opportunity for sustainable growth.
But Kian’s story began long before plastic recycling became a global concern—before ESG targets, carbon credits, or the circular economy buzzwords became axioms.
“I started recycling at the age of 10.”
“Some of you will remember the call of ‘Surat Khabar Lama!’, that good ole cry for old newspapers and recyclables.
My parents collected recyclables from house to house. We were part of the recycling ecosystem before we understood it academically.”
Despite the family’s deep roots in the recycling trade, Kian’s father had misgivings about the industry.
“He always told us to study hard and never end up as recyclers.”
“He felt it was dirty work, not respected. Ironically, that sentiment made me want to stay in recycling—to defend our family honour.”
After completing a degree in mechanical engineering and an MBA at Thunderbird University in Arizona under a Fulbright Scholarship, Kian returned to Malaysia with a mission to modernise the recycling sector.
In 2002, he founded Heng Hiap Industries Sdn Bhd (HHI), determined to fix the fragmentation he observed in the plastic recycling value chain.
“At the time, the entire process was split across different entities—each doing one part, from sorting and washing to extrusion and compounding,” he explained.
“It was inefficient, costly, and there was no standardisation. Quality dropped, costs rose, and recycled plastic got a bad name.”
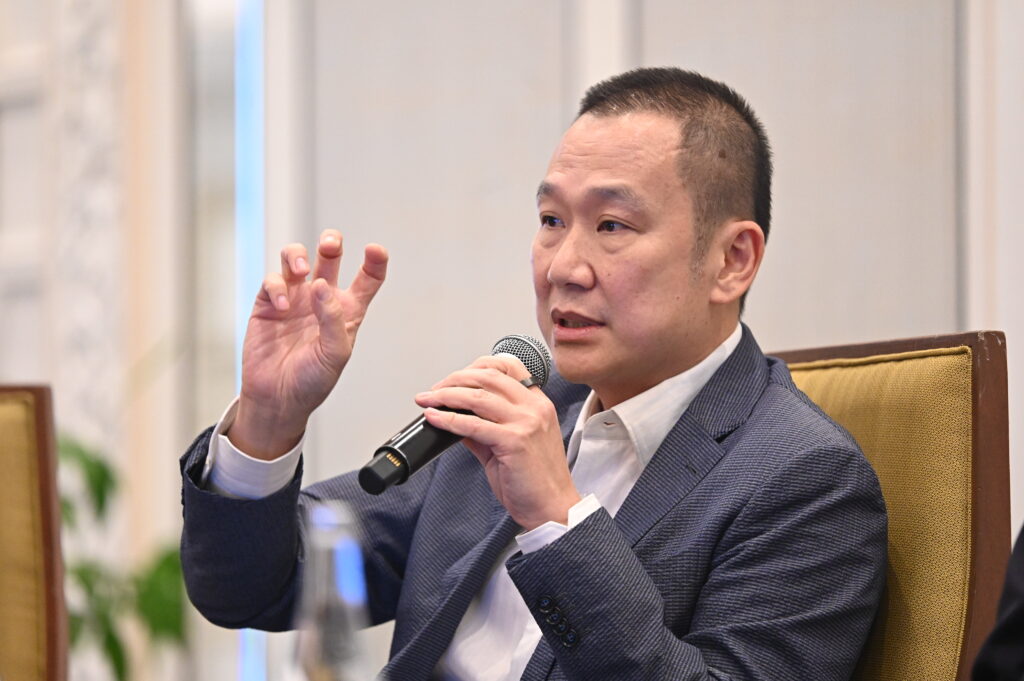
Rather than play by outdated rules, Kian built an integrated model. HHI would do everything in-house and end-to-end, from collecting to producing high-performance recycled resins tailored for global manufacturers.
HHI created internal standards to ensure consistency, traceability, and quality in every batch of recycled plastic.
“Once we integrated the value chain, we saw immediate results.”
“Labour costs dropped by 40%, logistics by 60%, and most importantly, we were able to create feedstock that’s consistent, customisable, and credible.”
Today, 70% of HHI’s output is exported to over 40 countries, powering the products of global household names.
Their clients span industries from consumer electronics to automotive and construction materials, who are seeking reliable, sustainable plastic resins that match—if not outperform—virgin plastic.
But it hasn’t all been smooth sailing. The early years nearly bankrupted the company.
“I underestimated the importance of execution and building the right team,” Kian admitted.
“It took time to get the business model right, and even more time to earn customers’ trust.”
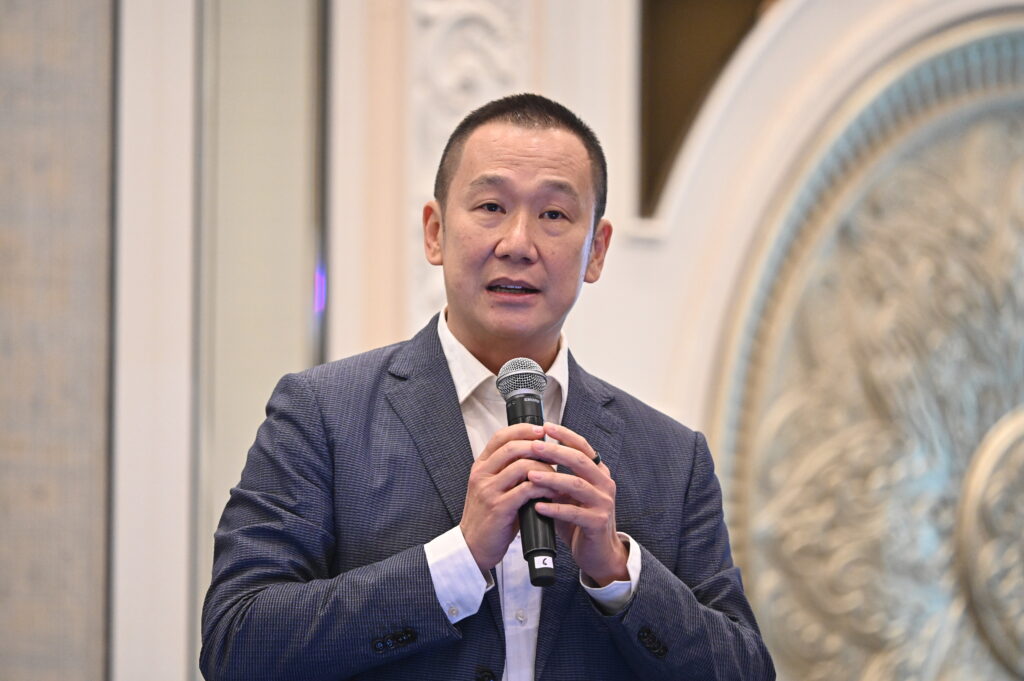
The experience has made him a strong advocate for integrating academia and industry. HHI collaborates with universities and education agencies to bridge the gap between technical knowledge and real-world application.
“If I had learned what I know now during university, I could’ve avoided a lot of pain,” he said. “We need a new kind of learning that combines academic theory with industrial realities.”
This philosophy underpins Kian’s vision for “Recycling 3.0,” the next evolution in HHI’s journey: a more innovative, circular plastic economy that integrates mechanical and chemical recycling to extract value from plastic waste even after multiple lifecycles.
“Plastic isn’t inherently bad.”
“Every time it changes shape or form, it generates value. Plastic becomes a problem only when it remains static—when it’s left in its final form, unused, for hundreds of years. That’s plastic pollution.”
To prevent that stagnation, HHI is pioneering a “7+1” cycle. Plastics can be mechanically recycled up to seven times before their molecular structure weakens.
After that, HHI employs chemical recycling through pyrolysis to convert the plastic into hydrocarbons—diesel, syngas, and naphtha—which can then be used to make new plastic, closing the loop entirely.
“We’re not afraid of a world with no new fossil inputs into plastics.”
“Because everything is still part of a hydrocarbon cycle. Solid plastic, liquid diesel, and gasified LPG are different forms of the same thing.”
This holistic approach to resource circularity isn’t just environmental—it’s profitable.
HHI’s innovative plastics are up to 50% stronger and 20% cheaper than unprocessed materials, often fetching prices higher than virgin plastics.
“We believe in the economics of innovation,” he added. “We don’t innovate for innovation’s sake. We innovate to solve real problems—technical, commercial, and societal—and ensure that what we do is sustainable in every sense of the word.”
“Part of that sustainability comes from securing a steady stream of feedstock.”
Today, HHI works with over 28,000 independent collectors across Asia, creating a “loyalty loop” that ensures materials are sourced in the right quality and volume. This supports a bottom-up model that’s been instrumental to HHI’s recycling success.
According to Kian, Malaysia’s plastic recycling rate is now at 35%, significantly above the global average of 11%.
Looking ahead, Kian envisions Malaysia playing a bigger role on the global stage.
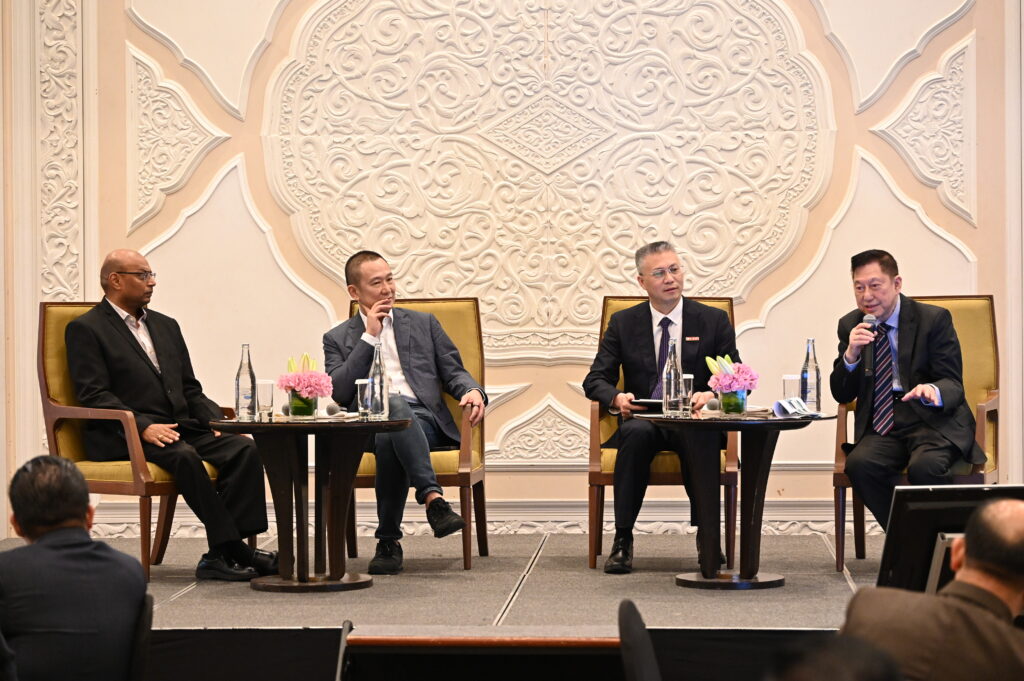
“We’re not too big or too small. We’re just the right size to test and scale bottom-up solutions.”
“If we get this right—if we can demonstrate a working 7+1 circular model—we’ll have something the world can follow.”
For someone whose journey began with a stern warning from his father to do anything but recycling, Seah Kian Hoe has come a long way. His motivation to defend his family’s honour may be the unexpected spark the world of plastics needs to shift from pollution to renewal.